Energy Efficiency: Crushing and Grinding
The U.S. has the largest Mining industry in the world, which accounted for 13.4% of the total U.S. GDP in 2007 (Economics, 2009). The Industrial Technologies Program of the U.S. Department of Energy (U.S. DOE) listed the Mining industry as one of the most energy-intensive industries (BCS, 2002). In fact, the Mining industry consumes about 5% of total U.S. energy (BCS, 2007). Crushing and grinding are attributable to such a high energy demand, in part due to an energy efficiency as low as 1% (Fuerstenau, et al., 2002). One of the most promising solutions to enhance such a low energy utilization is to take advantage of natural weaknesses in a rock (Fuerstenau, 1992). Multiplying internal flaws enhances energy efficiency by reducing the energy consumption in non-energy released areas inside of a particle (Tromans, 2008).
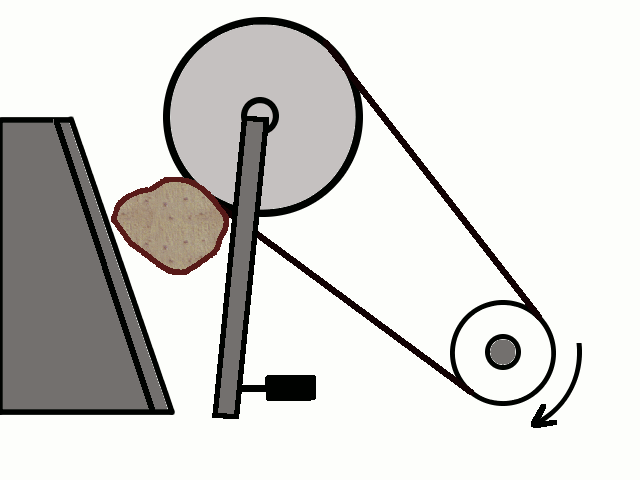
Jaw crusher
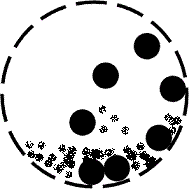
Ball mill
-
Mechanical breakage process for size reduction of particles
-
Rocks -> coals, metals, minerals, sands, and gravels
-
Cement clinkers -> fine particles
-
-
5% of total U.S. energy consumption & 13.4% of total U.S. GDP
-
Energy efficiency: as low as 1% (ref: BCS, 2007)
Energy Losses
Energy losses in crushing process are inevitable. Energy flux and surface energy production in comminution was initially introduced by Rumpf (1973). Rumpf explained each of the energy losses and the mechanism of surface energy production in comminution in terms of physical aspects using energy flow diagram. Most forms of energy losses were explained in the study, but the energy loss generated between particles or particle and other materials was ambiguous. Also, the kinetic energy term which is present after generation of new surface is not included in the explanations. In this background, we supplemented the energy flow diagram originally proposed by Rumpf (1973), and modified it as shown in the figure below. Considerable portion of mechanical energy input is consumed in frictional losses (1) along the wall or between particle and grind medium and/or between particles, as well as in viscous losses; (2) when grinding medium falls on loose bed. These two losses are main sources of heat dissipation. In addition, some portion of energy input is consumed via plastic deformation in particles and other mediums (Wu et al. 2004), and some remains in the particles after new surfaces are produced, which is called Helmholtz free energy in thermodynamic field (4) (Einav, 2007). Micro-plastic deformation (5) could be induced at the crack tip before fracture no matter how brittle particles are, and broken particles fly away in the form of kinetic energy (6) (Bergstrom, 1962; Wu et al. 2004). Once new surfaces are produced, there are complex interactions with surrounding in form of chemical reaction (8) or adsorption (9) (Wiederhorn, 1969; Rumpf, 1973). Besides, a small portion of energy is dissipated by energy coupling through radiation, acoustic emission or vibration of molecules (Luong, 1990). Therefore, the amount of newly produced surface is not same with that right after the fracture due to interaction with surrounding, and great care should be taken when measuring new surface area to evaluate energy efficiency.

Strategy 1 - Microwave-treatment before crushing
Dielectric materials undergo four types of polarization when exposed to microwaves: electronic, dipolar, ionic, and space charge polarization. These polarizations result in temperature increases, because stored internal energy is lost to friction (Gueguen, et al., 1994). A rock usually consists of several minerals that have different dielectric properties. Therefore, differential thermal expansion may generate internal defects along grain boundaries when a rock is exposed to microwaves (Santamarina, 1989). Moreover, no energy is wasted because only the responsive minerals are affected by microwaves (Jones, et al., 2005).
In fact, many researchers have been exploring this idea during the last decade to ease the process of rock breakage (Jones, et al., 2007, Jones, et al., 2005, Kingman, et al., 2004, Kumar, et al., 2006, Satish, et al., 2006, Scott, et al., 2008, Wang, et al., 2005). Although their studies showed promising results via the microwave treatment, they only focused on the aspect of differential thermal expansion between rock minerals. If a rock contains only “transparent” minerals as the granite does, differential thermal expansion may not be sufficient to induce any meaningful crack propagation. On the other hand, water molecules are dipole, and microwaves heat up water far more efficiently than it does on rock minerals (Gueguen, et al., 1994). In this background, we explored the following idea both experimentally and analytically: if a material is exposed to microwaves after being saturated, considerable number of cracks can be generated, thus the energy efficiency of the crushing and grinding processes can be enhanced. Figure below shows an example of study results. A manuscript about this study is currently under review.

Concept of microwave-treatment (left) and tensile breakage test results with/without microwave heating (right)